Tesla veut modifier des processus de fabrication vieux de 110 ans, afin d’ouvrir la voie à des voitures moins chères.

Tesla veut changer des pratiques de fabrication vieilles de 110 ans, c’est censé être une voie clé vers des voitures moins chères.
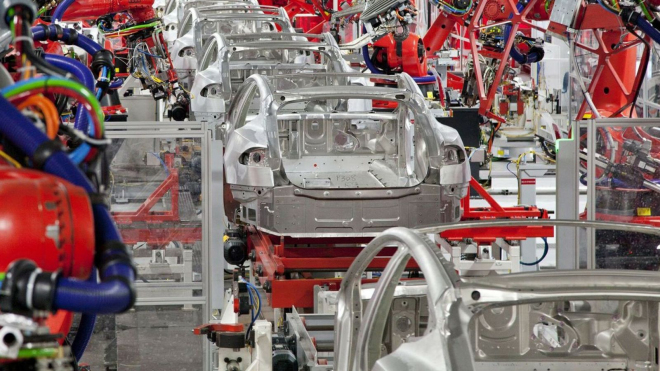
/
Tesla tente d’innover l’industrie automobile à de nombreux niveaux, sans exclure les processus de fabrication. Ceux-ci sont restés sensiblement les mêmes depuis 1913, mais les Américains ouvrent aujourd’hui la voie avec un procédé appelé Unboxed. Il suscite l’enthousiasme des uns et l’inquiétude des autres.
Le 1er décembre prochain, nous célébrerons un anniversaire important dans le domaine de l’automobile. C’est en effet ce jour-là, en 1913, qu’Henry Ford a installé la première chaîne de montage mobile dans son usine, changeant ainsi l’industrie et mettant l’automobile à la portée du commun des mortels. Avant son lancement, le modèle T se vendait environ 900 dollars. Avec le temps, cependant, son prix est tombé à moins d’un tiers, de sorte qu’après quelques mois d’épargne, même l’ouvrier qui l’avait fabriquée pouvait l’acheter. Il n’est donc pas surprenant qu’en 1923, plus de 2 millions de voitures de ce type aient été vendues.
L’invention de Ford est restée essentiellement inchangée pendant 110 longues années. Pendant cette période, l’automatisation n’a fait qu’augmenter, mais le principe du processus de production est resté le même. Au début du processus, il y avait une carrosserie fraîchement soudée, qui était ensuite équipée de portes et de pare-chocs et peinte. Les portes ont ensuite été retirées pour réaliser l’intérieur. Le groupe motopropulseur a également été installé. Au cours de ce processus, la voiture était suspendue sur une ligne, d’une station à l’autre.
Tesla considérait toutefois ce processus comme inefficace. La limite est la carrosserie elle-même, qui ne permet qu’à un nombre limité d’employés de travailler à l’intérieur. L’accès par l’extérieur n’est pas non plus idéal, car il ne faut pas oublier que les voitures modernes mesurent 4,5 à 5 mètres de long et 2 mètres de large. C’est pourquoi les postes de travail individuels doivent être suffisamment spacieux. Cela entraîne un gonflement des halls, ce qui coûte également de l’argent.
Peut-on changer cette méthode vieille de 110 ans ? Selon Tesla, oui. En mars dernier, le constructeur automobile a présenté aux investisseurs une nouvelle méthode appelée « Unboxed ». L’idée est de décomposer la voiture en modules individuels, qui seront assemblés séparément sur chaque site. Alors qu’une équipe sera chargée du côté gauche de la carrosserie, par exemple, une autre s’occupera du côté droit, une troisième de l’avant de l’habitacle et une quatrième de l’arrière. La cinquième équipe travaillera sur le groupe motopropulseur, tandis que la sixième équipe assemblera le tout. Ainsi, un certain nombre de pièces de différentes voitures, même de différents types, peuvent être créées séparément, si leurs modules sont compatibles. La charge de travail des ouvriers et des machines pourrait donc être extrêmement élevée, surtout si des personnes peuvent se charger de la production des différents modules au fur et à mesure des besoins.
Cette idée a bien sûr fait grand bruit dans le monde. Tesla promet une augmentation de 44 % de la productivité, ainsi qu’une amélioration de 30 % de l’utilisation de l’espace dans ses usines. La production de voitures devrait augmenter de 50 %, tandis que les émissions devraient également être réduites de 40 %. Le constructeur automobile devrait ainsi enfin tenir son engagement, à savoir une voiture électrique abordable à partir de moins de 30 000 dollars, soit environ moins de 650 000 couronnes.
Cependant, les experts considèrent que l’ensemble du processus est risqué et qu’il « ne fonctionnera pas tant que la production de ces grands modules ne sera pas entièrement synchronisée et que les blocs terminés n’arriveront pas au bon moment pour l’assemblage final ». De même, on peut se demander s’il sera possible pour différents sites de produire des voitures différentes lorsque, par exemple, le style de la carrosserie ou les dimensions diffèrent. « À mon avis, c’est pratiquement impossible », a déclaré Hide Oba, qui a déjà travaillé à la mise en œuvre des processus de fabrication de Toyota, à ce sujet.
Par ailleurs, il convient de rappeler ce qui pose le plus de problèmes à Tesla. Ce n’est pas tant la vitesse à laquelle ils produisent leurs voitures, mais la mauvaise qualité. Par exemple, les panneaux intérieurs de nombreuses voitures ont été remplacés. La peinture tragique est un chapitre à part. Désormais, chaque partie de la voiture est peinte séparément. Il peut facilement arriver que le représentant de la marque vous pousse à reprendre une voiture dont la partie gauche est plus claire et la partie droite plus foncée, et dont l’intérieur est blanc d’un côté et noir de l’autre.
Il sera donc intéressant de voir comment tout cela va se dérouler. Nous devrons attendre un peu pour les premiers résultats, car le nouveau processus ne devrait pas être intégré à la nouvelle usine de Monterrey, au Mexique, avant la fin de l’année prochaine. Bien entendu, nous souhaitons bonne chance à Tesla, car si elle réussit, elle changera l’industrie comme l’a fait Ford. Nous craignons toutefois que cette idée ne doive être reprise par quelqu’un de plus consciencieux, qui ne verra pas d’inconvénient à fournir régulièrement et sans cérémonie des déchets à des gens pour des millions de couronnes.
L’idée de Tesla ne semble pas mauvaise. Cependant, nous sommes un peu inquiets de ce qui sortira à la fin de la chaîne de montage pour une marque qui est capable d’échanger même les décors intérieurs de la même voiture, où les travailleurs peuvent voir les deux côtés de la voiture juste en face d’eux. Photo : Tesla
Source.
Tous les articles sur Autoforum.cz sont des commentaires exprimant l’opinion du rédacteur ou de l’auteur. À l’exception des articles marqués comme étant de la publicité, le contenu n’est pas sponsorisé ou influencé de quelque manière que ce soit par des tiers.